ITER Central Solenoid Fabrication
General Atomics is fabricating the Central Solenoid Modules for the international ITER project, an unprecedented scientific partnership that aims to demonstrate the feasibility of fusion power as a clean-energy resource on a global scale. As part of this project, GA has developed a range of specialized manufacturing capabilities.
ITER Central Solenoid Fabrication Facility
6,000 sq. meters of temperature-controlled production space
Coil Winding
The Central Solenoid will consist of six stacked modules surrounded by a support structure. Each of the six modules is fabricated from approximately 6,000 meters of niobium-tin (Nb3Sn) conductor. The steel-jacketed conductor is wound to form six separate hexapancakes (6 layers) containing 14 turns in each layer. The seventh spool is wound to form a quadpancake (4 layers) containing 14 turns in each layer.
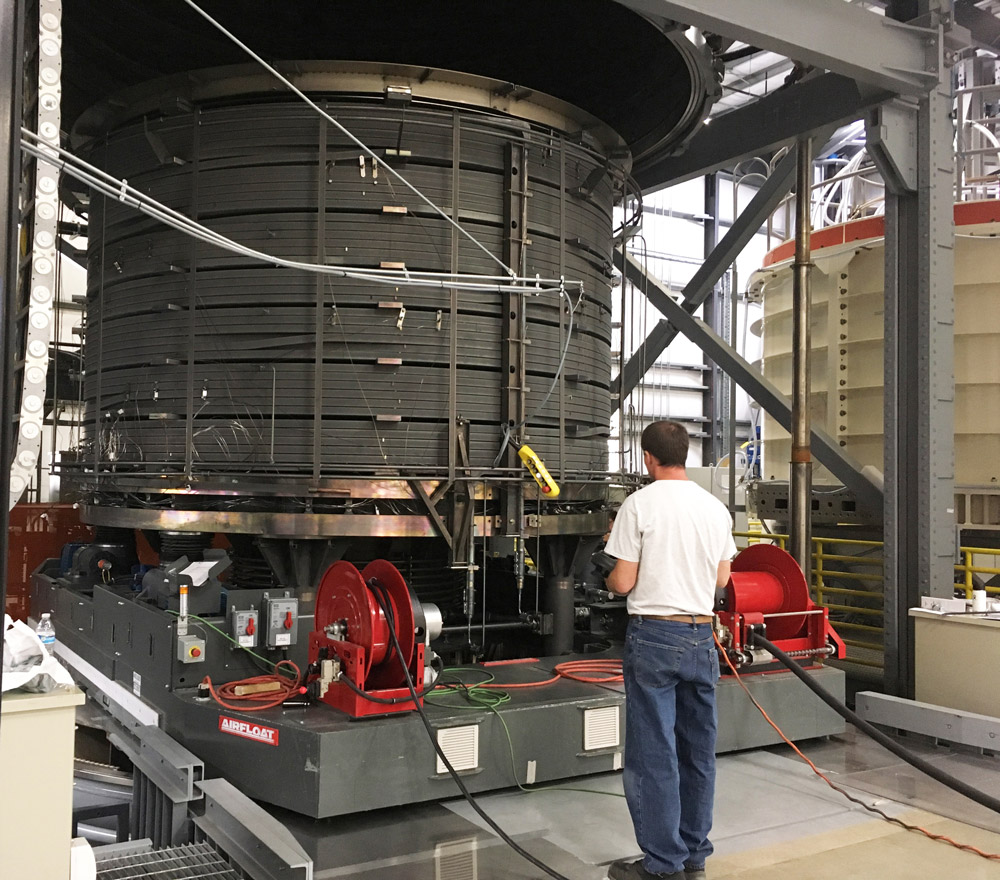
Coil Joining
The conductor cable in each hex or quad pancake is then carefully spliced to the next. This is performed by removing the steel jacket from the ends of each coil and stripping the chrome from the conductor strands using a reverse plating process. After splicing the conductor cables together like a rope, a new steel jacket is welded over the splice joint. Fittings for the helium coolant system and other connections are also added at this stage.
Superconducting Coil Heat Treatment
To create the superconducting material inside the module winding, the module must be carefully heat treated in a large furnace, which functions similarly to that of a convection oven found in many kitchens. The benefit of the convection oven is the ability to shorten the overall process while maintaining uniform "cooking" of the module. The module temperature within the furnace changes at a rate of five to six degrees Fahrenheit per hour, making both the heating and cooling processes very time consuming. Inside the furnace, the module spends approximately ten-and-a-half days at 1,060°F and an additional four days at 1200°F. The entire process takes about five weeks.
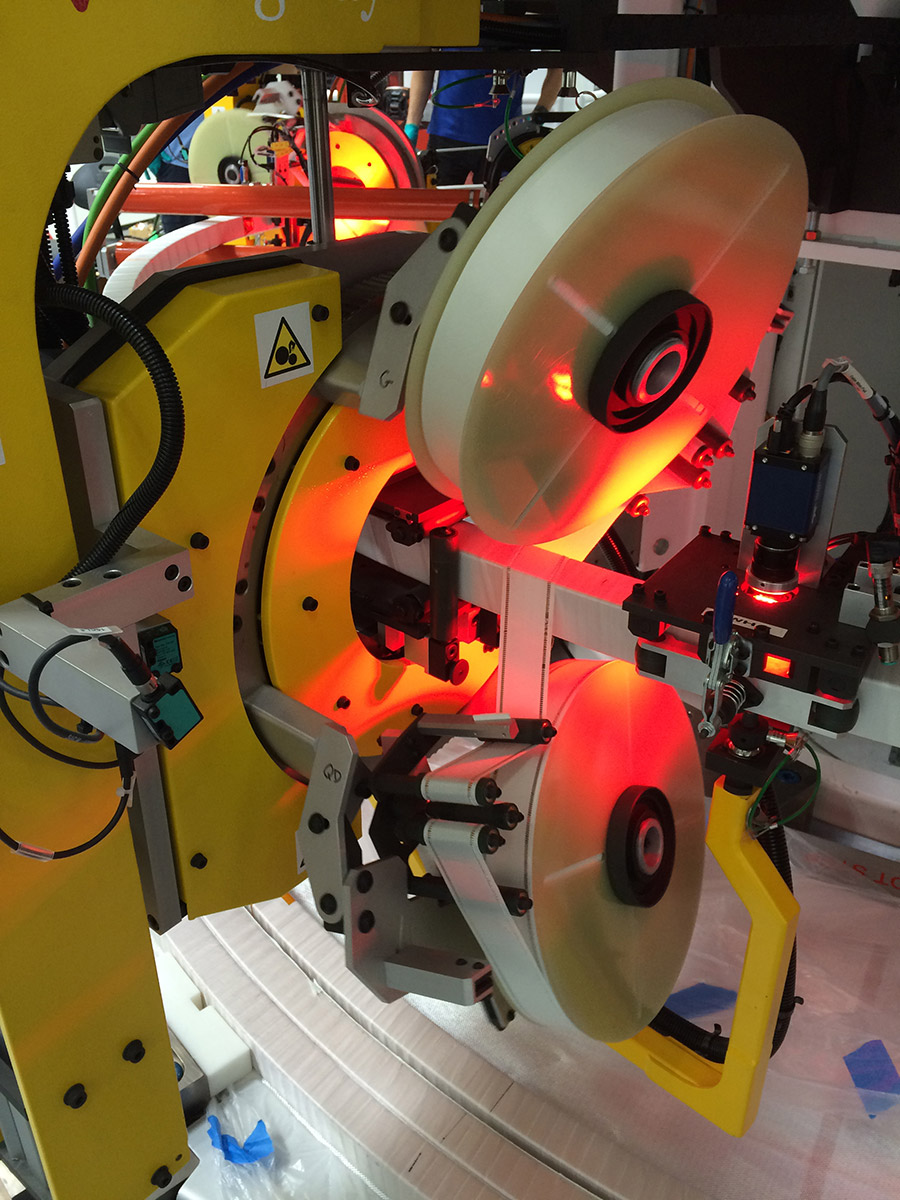
Coil Insulation
Conductor insulation ensures that electrical shorts do not occur between turns and layers. During turn insulation, the module needs to be un-sprung without overstraining the conductor, which is now strain-sensitive due to heat treatment. Each 110-tonne module must be lifted and its individual turns released for wrapping with fiberglass/Kapton tapes. To perform the wrapping, the turns of the module are stretched like a slinky, allowing the taping heads to wrap the insulation around the conductor. The module is reassembled exactly as it was wound and joined together. Wrapping the entire 3.5 miles of conductor for each module takes about four months using two shifts per day. During this time, 180 miles of tape is applied.
Once the individual turns are wrapped, the external module surfaces are then wrapped with ground insulation. The ground insulation consists of 25 layers of fiberglass and Kapton sheets. The materials are precisely placed to ensure protection of the coil against 30,000 volts occurring during a fault. The ground insulation must also tightly fit around complex coil features, such as the helium inlets.
After insulation, the module is enclosed in a mold, and 3,800 liters of epoxy resin are injected under vacuum, to saturate the insulation materials and prevent bubbles or voids. When hardened at 260F, the epoxy fuses the entire module into a single structural unit.
Cryogenic Systems & Cold Testing
The final step for the module fabrication is cold testing at 4.7 K with 48.5 kilo-amps, which is comparable to the operating conditions inside the ITER reactor. The insulation is tested to 30 kilovolts, and a fast discharge test is conducted to ensure the module can dump its stored energy in just 6 seconds. When fully assembled, the six-module Central Solenoid and associated structures will be 13 meters tall, weigh 1,000 tonnes, and be capable producing a magnetic field of 13 Tesla, making it the largest pulsed superconducting magnet ever constructed.